Big Changes Coming to Prineville’s Wine Box Operations
[February 24, 2023] Prineville’s successful wine box business is growing, and a new inline manufacturing system will help the crew take it to the next level this summer.
A New High-Speed Glue Applicator Specifically Designed for Small Parts
Greg Rivers, Madras Fabricator, completed step one by building a new glue applicator for the line. “Greg is a highly skilled fabricator, enjoys the challenges of precision fabrication, and takes a lot of pride in the machines he produces,” said John Carson, Fabrication Manager. “Thank you, Greg!”
“The new glue conveyor is designed after one that we already have at our Redmond facility,” Brad Bolton, Designer, said. “However, this machine needed to handle an 11-½” part length. The design challenge was containing the short part and transferring it through glue heads while keeping it stable at high speed.”
“The machine will edge glue one or both edges,” Brad said. “It will also face glue one or both faces and top glue. The plan is to feed one part per second.”
The Continuous Flow Process Will Be Four Times Faster
“We need the new glue applicator to tie the moulder into the Radio Frequency (RF) laminator, so we have a continuous flow,” Brad said. “Currently, they run material through a moulder, stack it down, inventory it, then bring it back to the laminator to run. We expect the inline system to be four times faster than the current process.”
“Although our roll coater did a fine job for glue spread, it is a slow process to feed and get to the layup table,” Kim Dixon, Prineville Site Manager, said. “Moving the moulder inline with the laminator will reduce the risk of producing off-spec or off-grade material.”
“We will rebuild the backend of the line during Phase 2 of the project,” Kim said. “It will include a new Precision End Trim (PET) saw and a panel rip.”
Well Done, Prineville Lamination
“We have had a very experienced lamination crew for the past four years with little to no issues with the prep work,” Kim said. “Job well done, and thank you.”
“The production team in Prineville has performed flawlessly since we have been doing this business directly with M. Calosso & Son,” said Mark Schongalla, Sales. “As you can imagine, with all of these small parts at a fairly high volume (11 – 18 trucks per year), anything we can do to decrease labor and processing time is critical.”
“Adding an inline moulder, the Bright Wood-built glue conveyor, and a new layup area will reduce the overall processing times and increase our efficiency big time,” Mark said. “We are about to add several more trucks of orders into the file, so we will soon be realizing the benefits of these improvements.”
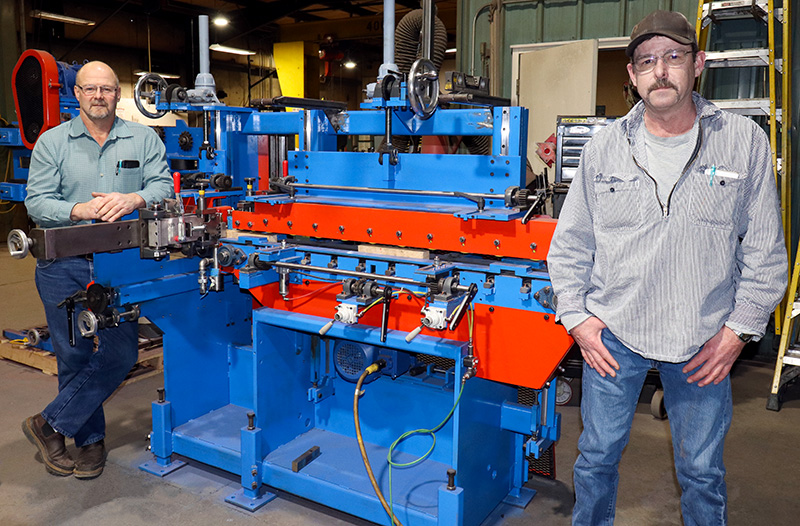
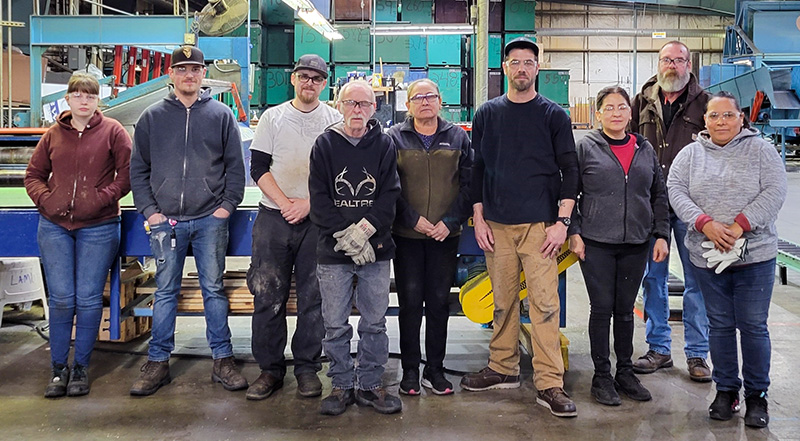